the module recognizes and rejects components which are deformed beyond a permissible level. This eliminates the need for the traditional function and X-ray tests used to identify open solder joints on deformed components. With the coplanarity measurement, electronics manufacturers can minimize expensive repairs after the placement process, making the SIPLACE 3D Coplanarity Module an important tool for the zero-defect production of safety-critical applications.
以其3 D Coplanarity模块,ASM Assembly Systems GmbH & Co. KG提供了新的选择SIPLACE装备SX-Series机器。用三点激光检测missing balls or bent leads (BGA焊点缺少,引脚变形),新的三维Coplanarity模块现在也能检测大BGAs和QFPs的平面性。不到500毫秒(100个QFP组件为基准),速度比传统的二维coplanarity测量技术显著提高。
模块识别形变超出允许的水平的零件。不需要传统的x射线测试,就能识别变形元件的OPEN SOLDER.共面性检测让电子产品制造商能最大限度地减少昂贵的后焊处理。SIPLACE 3D coplanarity模块是一个重要的0缺陷测试工具保证严格安全的制程。
The SIPLACE 3D Coplanarity Module is an option for the placement of large BGAs and QFPs on SIPLACE SX placement machines equipped with SIPLACE CPP MultiStar or SIPLACE TwinHead heads. In addition to the standard component recognition and inspection with the SIPLACE digital vision system, the 3D Coplanarity Module use a 3-point laser measurement system to check the leads or balls of BGAs for height variations relative to the ideal placement level, i.e. for deformations. Since the new 3D laser measurement also minimizes any production performance slowdown, because the new 3D laser measurement takes only a fraction of the time required by traditional 2D methods. On a QFP 100, for example, the system recognizes in less than 500 milliseconds whether any component leads were deformed beyond a certain tolerance level defined for this specific component type. Any components recognized as deformed beyond acceptability are discarded or optionally set aside. This significantly reduces the possibility of open or weak solder joints and the costs associated with post-production function or X-ray testing – an important step towards zero-defect production, particularly for manufacturers of safety-critical applications.
High delivery quality with automatic defect analysis
The SIPLACE 3D Coplanarity Module also supports automated defect analysis by storing all information about discarded or rejected components in the form of images. The system displays the component profiles graphically and highlights faulty leads. This information can then be used to work with component suppliers on making improvements.
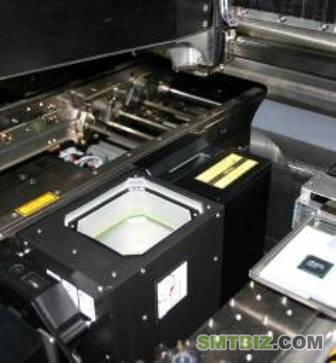
The new 3D Coplanarity Module now also verifies the planarity of large BGAs and QFPs, in addition to verifying missing balls or bent leads via a 3-point laser measurement.
More information at www.siplace.com.
ASM Assembly Systems
At the beginning of 2011, the SIPLACE team (formerly Siemens Electronics Assembly Systems) became a business unit of ASM Pacific Technology and operates now as ASM Assembly Systems. With its SIPLACE machines and innovative manufacturing concepts, ASM Assembly Systems GmbH & Co. KG is the world’s leading manufacturer of surface mount technology (SMT) placement machines and solutions. Since its beginnings in 1985, the company has installed almost 25,000 placement machines at over 2,500 customers all over the world. Electronics manufacturers in all industries such as telecommunications, automotive, IT, consumer electronics and automation use and depend on SIPLACE's broad portfolio of solutions and services.