波峰焊和热风刀制程指南
提高含有通孔引脚器件、表面黏着器件(SMD)及通孔引脚器件和SMD组合的电路板波峰焊性能的技术,包括具有革新性的焊波流体动力学,以及热风刀去桥接(debridging)系统。
典型的波峰焊系统通常包括助焊剂施加台(波峰式、泡沫式或喷雾式)、使用压板(platen)或强制对流的预热部份、焊膏槽(带λ波、曲线波或双波)以及去桥接热风刀。根据系统的不同,实际的情况会有所差别,但一般都包括助焊剂密度监控、指形传送器、用于指形传送器的指形方案、指形清洁器、预热部件和焊膏槽。
预热部件 印制电路板在遇到焊波之前,要藉由预热来升高装配温度(表1)。无论是压板还是强制对流预热方式,都有几个重要功能。预热有助于达到并保持助焊剂活化温度,以便去除锈蚀,并在焊接中使焊点湿润。预热还可干燥用于稀释助焊剂的试剂和溶剂,如果不进行干燥,就可能在焊接过程中产生气泡。它还可干燥电路板所吸收的水分和电镀液,否则就会因为焊膏的沸腾而发生溅射,使焊膏中进入蒸气,形成空心焊点和气孔。温度的逐渐上升有助于减小器件和整个设备受到的热冲击。遇到焊波时,受控的预热可最大限度地减小电路板在遇到焊波时的变形。
表1:预热参数(从预热器出来的PWA顶端温度)
最后,传送器的速度可以得到提高,因为藉由对设备进行预热,可以缩短将器件引脚和焊盘加热至湿润温度所需的时间。从理论上讲,将器件预热到湿润温度可极大地提高焊接速度,但实际情况并非如此,因为在移动的表面施加熔化的焊膏时,会受到机械方面的限制并产生液压效应。
对多层电路板而言,建议的预烘干温度是105℃,持续2至4小时。需要注意的是,烘干时,不要将电路板迭放在一起。如果迭放在一起,内层的电路板就会被隔热,达不到预烘干的效果。建议将电路板放在一个对流炉里,每块电路板之间最少相距3mm。
只有当电路板上出现气泡时才进行预烘干。过度预烘干会产生较厚的表面氧化层,从而使湿润时间较长,甚至不能润湿。参考制造商提供的零配件数据,有助于确定具体电路器件的预热要求,从而得到最好的焊接效果。
焊波类型和焊膏流特性
对包含标准通孔引脚器件的电路来说,λ波效果很好。
印制电路组件(PWA)进入λ波后,焊膏流向与PWA移动方向相反,从而在器件引脚周围形成涡流。涡流可以洗掉氧化物和助焊剂残余物。去除了残余物,焊点达到湿润温度后就能润湿。
在λ波出口处,焊膏流向与电路板移动方向一致。如果PWA以退波(receding wave)速度退出焊波,焊膏就能适当地得到剥离(peel back)。
焊接SMD所用的芯片波(chip wave)是窄带高能量波,可在SMD引脚和焊盘周围的焊膏中环绕。这种涡流能确保焊膏渗透到器件的所有引脚和焊盘中,即使是密集数组的SMD。该波也能去除电路板上的部份氧化物和助焊剂残余物。电路板藉由芯片波之后,再藉由λ波即可完成焊接过程。
组件的放置
电路板上组件的合理取向可大大减少焊接缺陷,如桥接和焊痕(shadow)。一般地,轴向引脚组件按任意方向放置都不会引起焊接缺陷。对于板上黏着的SIPS、DIPS、四方封装、直插式连接器(in-line connector)以及所有类型的密集数组SMD,如果组件放置不当,将会产生严重的焊接缺陷(见“组件布局建议”)。
黏着热风刀
对于高密度电路、小体积器件、或以高速度焊接器件时,都可使用去桥接热风刀,作为标准设备或现场更新设备。位于焊槽出口处的热风刀有几个显著的优点。在PWA退出焊波、焊点仍处于熔融状态的情况下使用热风刀。简言之,喷向PWA底部的热气流,可消除焊点的黏连、使焊点成型、填充通孔中的气泡、去除焊点的桥接、除去多余的焊膏、暴露湿润问题、并修复开裂的焊点。
去除高密度电路和小体积器件焊点的桥接,可以减少返修量,提高生产率。在装有去桥接热风刀的大型生产环境系统中,焊接缺陷率可低至2PPM到20PPM。
检验也同样非常重要。肉眼检验合格的焊接,其通孔中可能存在气泡,这样电路板在使用中受到应力时就会出现故障。热风刀利用直接喷射到焊点上的热气流压力检验每一个焊点,检验速度达到每秒100个焊点或更高。
以1,000ergs/cm▲2▲的速度(吹掉多余焊膏大约所需的力)喷射的热空气不会对良好的焊接造成影响,却可以暴露可能隐藏气泡的不良焊接。
热风刀使已敷上焊膏的通孔焊点发生回填(refilling),这种通孔焊点处容易引起漏气(outgassing)问题。热风刀使空穴暴露出来,仍处于熔融状态的焊膏藉由毛细作用(wicking)进入孔中,就发生了回填。焊点发生回填后,就好象一个未焊的焊盘位于器件引脚周围。藉由进一步的检验,可以发现,焊膏已经一定程度地进入通孔中。根据所采用的检验标准,如果引脚和通孔湿润良好,则认为焊点合格。
热风刀的另一个优点在焊接SMD时非常明显。玻璃/环氧树脂基底、组件引脚、焊盘及焊膏的膨胀系数各不相同。如果引脚和焊盘上的焊膏过多,就会使焊点凹面产生过大的应力,使焊接过早出现问题。热风刀能使焊点定型、去除多余的焊膏并使焊点延展性更好,有助于消除热应力疲劳和机械应力疲劳。
热风刀动力学
热风刀向组件底部喷出一条窄窄的热气流(0.46mm)。根据电路板上器件密度、类型和取向的不同,热风刀温度通常在260℃至274℃,压力在4psi至20psi。
为提高制程效率,可对几个热风刀参数进行调节:
与电路板底部的冲击角(与水平方向成40°至90°)和距离(尽可能靠近); ‧若发现焊膏从电路板上部溅出,则热风刀上的气压应以1psi的增量减小,直到实现去桥接而又不会过吹; ‧对所有类型的电路组件,在5psi至10psi的气压和426℃的温度下,都会有较好的结果。标准参数见表2。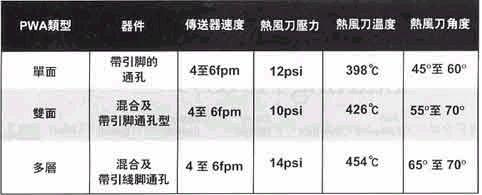
?
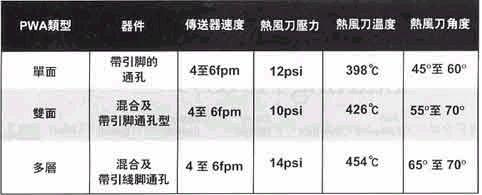
?
表2:高性能热风刀初始设置参数
焊接制程参数各种焊接参数以不同的方式影响波峰焊过程。为建立有效的焊接制程监控程序,需了解各参数的作用。
预热预热不足将妨碍热风刀的有效工作,而且会使PWA在预热和焊波之间的温度变化率(ΔT)过高。
热风刀高度一般,热风刀离PWA底部越近,效果越好。因为这样热空气只需较小的压力就可向焊点进行有力的喷射,而且离开热风刀出口后温度下降较少。
热风刀压力热风刀压力决定了焊接处所受的应力大小。如果压力不足,就不能充分检验焊接的质量;而压力过大,则会导致焊点凹面上产生应力线。在极端情况下,通孔中的焊膏会被吹落。
焊波高度如果焊波高度不足,尤其是焊接SMD时芯片波高度不足,会使焊接不充分或焊膏不能充分应用。还会发生通孔中焊膏不足的情况。
传送器速度传送器速度会影响焊接制程中几乎所有其它参数。藉由预热器的时间决定了PWA吸收热量的多少。速度越慢吸收热量越多,越快则越少。藉由焊接波的时间影响焊膏渗透通孔的程度。另外,焊波是热风刀的二级预热器。传送器速度决定了热空气冲击时间的长短。速度较慢则热风刀工作时间较长,一些情况下可以减小压力。
检验在完成热风刀焊接后的检验中,可以发现,针孔、气孔以及焊接变形都大大减少,这是因为热风刀即使在漏气时也会使焊点凹面重新成型。漏气的焊接焊点凹面很小,有时焊点会凹进通孔中。若润湿良好,而且超过75%的通孔中都充满了焊膏,则认为焊接合格。由于热风刀能够去除多余的焊膏,因此产生的焊点更小、更具延展性,这有利于消除使用过程中的机械疲劳。
经热风刀处理后的焊点不再象未经处理时那样具有表面光泽。仔细检验会发现焊接表面具有鳞状的纹理。这是焊接表面藉由热风刀处理后的共同特征。这种纹理结构比未经热风刀处理的表面更好、更坚固。
容易污损的“没有焊膏”的焊接处要对引脚和焊盘去湿。这可减少无焊膏焊接(焊膏侧)、引脚弯曲、引脚突出及组件遗漏或翘曲(组件侧)等缺陷的发生。
由此可见,最终结果是减少了焊接后的检验工作,PWA的处理过程也缩短了,同时提高了焊接成品率。
Sidebar组件布局建议下面是对电路板布局的一些建议,有助于减少焊接缺陷:
长方形电路板的较长边应与传送器的导轨平行。若难于做到,则在焊波中使用一个电路板支架,或在电路板上采用一个跨度超过7英寸的加劲杆。
使用热质量相同的组件可以提供更均匀的加热。若难于做到,则需要增加顶端的预热并降低传送器速度。
对电路板进行布局时,应使带直插式引脚的组件与传送器传送方向一致。
尽可能使密集的电路线与传送器传输方向一致。
自动插入设备的引脚不要过多。
在符合经济性的前提下,尽量使四方封装器件远离SMD器件。